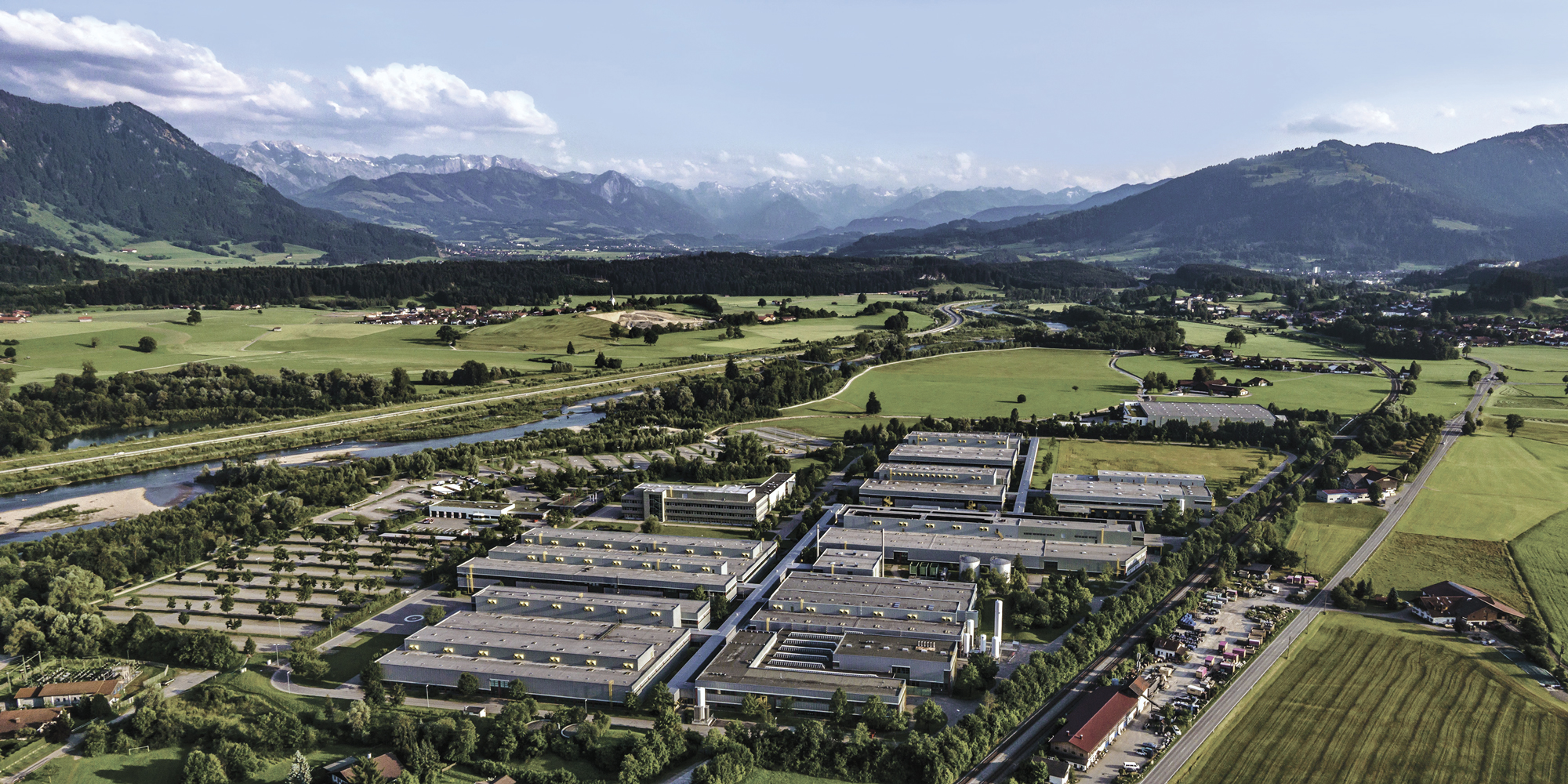
Tecnología y Sociedad
Bosch transforma sus plantas en fábricas inteligentes para dominar la producción
Automatizar y medir cada cosa que sucede en sus plantas no solo le ayudarán a ser más eficaz sino que ese conocimiento le permitirá liderar el nuevo negocio de la fabricación inteligente
Crédito: Laetitia Vancon.
Media docena de jóvenes ingenieros, principalmente hombres, se encuentra en una luminosa oficina diáfana revolviendo una montaña de código. Estaciones de trabajo con múltiples monitores reposan sobre las mesas abarrotadas con portátiles, tabletas y cascos. Pero, no es una start-up tecnológica. Es una habitación dentro de la planta automovilística de Bosch cerca de Immenstadt (Alemania). Hoy, estos trabajadores están destapando las ineficiencias inmediatas de producción y desarrollando sistemas que esperan que para el año que viene permitan que las máquinas de la fábrica autodiagnostiquen los problemas, pidan proactivamente piezas de repuesto y se anticipen a los trabajos de mantenimiento necesarios con horas o hasta semanas de antelación.
A través de un gran ventanal de la sala de ordenadores que se asoman a la zona de fabricación, se observan filas de máquinas ronroneando una melodía de percusión al producir pequeñas piezas destinadas a empresas automovilísticas que incluyen BMW, Wolkswagen y Tesla, como boquillas de inyección de combustible, sistemas electrónicos de control de seguridad y sistemas de frenado automático.
Encima de cada máquina se encuentra un semáforo que muestra su estado de eficiencia, y unos grandes monitores elevados muestran datos de producción en tiempo real. Los operadores acceden con tabletas a los datos captados por los más de 100 sensores de cada máquina. Los encargados ven valores desglosados de cada minuto de todo desde la electricidad hasta el aire comprimido. Pueden obtener el desglose de cualquier máquina individual, e incluso de herramientas individuales. Todo lo rastreable es rastreado por etiquetas de identificación por radiofrecuencia (RFID, por sus siglas en inglés). Las pantallas muestran no sólo cifras en forma de gráficos sino también unas imágenes visualmente precisas, algo reminiscentes a los dibujos animados, de las máquinas reales y de la planta de producción.
Para Bosch, existe cierta urgencia en transformar su sistema ya eficiente de producción en algo más automatizado. Con sus 375.000 empleados a nivel mundial, este productor de máquinas de líneas de montaje, neveras y mucho más de 130 años de antigüedad ha de aproximarse más a la fabricación conectada para seguir compitiendo. Los altos costes de la mano de obra y de la energía hacen que las operaciones de este tipo de plantas resulten muy caras.
Foto: Dentro de la fábrica. Crédito: Laetitia Vancon.
Foto: Daniel Kirchmann trabaja en el código para analizar automáticamente el rendimiento de máquinas de la línea de montaje. Crédito: Laetitia Vancon.
Es un cambio que los ejecutivos afirman que es igual de disruptivo que la revolución de la producción masiva del siglo pasado. Obviarlo sería como perderse el cambio de la fotografía de carrete por la digital, según el vicepresidente ejecutivo de Industrias Conectadas de Bosch, Stefan Assmann. "Kodak podría servir de advertencia para que las empresas realmente realicen esta transición. El principal riesgo consiste en no trabajar en [la transición] y creer que los viejos buenos tiempos van a continuar", señala.
Foto: Un cartel se lee "Industria 4.0", una abreviatura europea para la fabricación avanzada. Crédito: Laetitia Vancon.
Los esfuerzos de la empresa se perciben por todas partes. Dentro de la cafetería, los cajeros han sido reemplazados por platos y vasos con etiquetas RFID. Fuera, un cortacesped robótico rasura el símbolo de Bosch en el jardín.
En la planta, la productividad de las líneas de montaje clave han mejorado en un 20% al año desde 2012. Y para 2020, Bosch calcula que tecnologías como las líneas de montaje conectadas, el mantenimiento predictivo y las máquinas con cierto grado de consciencia añadirán 1.000 millones de euros en ventas, junto a una cantidad similar en ahorros operativos. "Sólo hay un propósito, ganar dinero", afirma el administrador de la planta, Rupert Hoelbacher, sobre el impulso para hacer que esta y las otras 10 plantas de Bosch que dirige sean más eficientes, más conectadas y más inteligentes.
Arriba: Un trabajador de la última línea de montaje de dos sistemas de seguridad fabricados en la planta: sistemas de frenado automático y programas de estabilidad electrónica. Abajo: Unos monitores muestran informaciones sobre la gestión energética de cada máquina de la planta. Crédito: Laetitia Vancon.
En una pequeña sala de reuniones en la fábrica, Hoellbacher explica que los límites de la producción convencional se están volviendo evidentes, incluso con robots en la línea de montaje. Sólo se puede exprimir una máquina hasta cierto punto a la hora de medir y compensar unas variaciones minuto a minuto de la temperatura, el tiempo de ciclo o la frecuencia de las vibraciones con una sensibilidad y velocidad que superen las capacidades humanas.
Foto: Rupert Hoellbacher gestiona 11 plantas de Bosch. Crédito: Laetitia Vancon.
Foto: Unas máquinas terminan de fabricar boquillas de inyección de combustible. Crédito: Laetitia Vancon.
Para cumplir con los objetivos de productividad de la empresa, las líneas de montaje al completo han de monitorizarse con software capaz de analizar complejos datos a velocidades de superordenador para detectar los procesos operativos más eficientes, anticiparse a las averías y preparar soluciones. Lograr que funcione de forma óptima es un enorme reto, pero la mayoría de las máquinas de las fábricas Hoellbacher ya están conectadas y transmiten datos al centro de datos de Bosch en Stuttgart (Alemania).
Para finales de este año, habrá 6.000 máquinas en 11 plantas de las que se extraigan datos cada segundo, con el día de cada máquina resumido y analizado en un informe automatizado de 20 páginas. Bosch tiene 250 fábricas en todo el mundo, y el plan de la empresa es introducir las mismas tecnologías en todas ellas.
Foto: El interior de unas máquinas de fabricación de la línea de montaje. Crédito: Laetitia Vancon.
En la planta de producción, Arnd Kolleck, que se encarga del esfuerzo en tecnologías de la información, habla de un producto de Bosch que ofrece un vistazo al futuro: iBooster. El dispositivo, que la empresa vende a las automovilísticas, ajusta la presión del frenado en frenos convencionales y sistemas de frenado regenerativos, que son empleados a menudo para convertir la energía cinética en energía en vehículos híbridos o eléctricos. También puede acumular la presión de frenado sin la participación del conductor, para anticiparse a cualquier cosa desde un suave frenado hasta una parada de emergencia antes de que se le ocurra ni siquiera al conductor pisar el pedal del freno.
Foto: Unos hornos industriales aplican calor a unas piezas de metal fabricadas por moldeo de inyección. Crédito: Laetitia Vancon.
Producido por primera vez en 2013, iBooster está instalado en más de 350.000 vehículos. Este año fue actualizado con una nueva prestación que se conecta mediante el wifi del coche con la red doméstica del conductor y envía detalles diagnósticos y de frenado a Bosch. Kolleck afirma: "Ahora sabemos que el propio conductor sobre cómo y cúando frena ", y se apresudra a añadir que los datos son anónimos.
Con estas datos, Bosch puede prototipar rápidamente nuevo hardware y software para versiones futuras de iBooster que se ajusten mejor a los perfiles de los conductores y los requisitos de los clientes. También puede minar los datos para elaborar otras aplicaciones o productos de conducción autónoma. Se incluyen aquellos que emplean en sus propias plantas de producción, donde robots que se especializan en la entrega y la fabricación de piezas, cada se desplazan más con autonomía e interactúan en estrecha proximidad con trabajadores humanos.
Arriba: Un tablero muestra el rendimiento actual de la planta de producción. Abajo: Los productos son escaneados automáticamente al pasar por esta puerta. Crédito: Laetitia Vancon.
"Lo que aprenderemos del tráfico urbanos se puede aplicar a interlogística de una fábrica", explica Assmann. Con conocimientos derivados de la adición de tecnologías de sensor a los coches y la recopilación de los datos resultantes, pueden "dotar a los robots de ojos, oídos y sentimientos", añade.
Assmann planes para estos datos que van más allá de las aplicaciones internas de Bosch. Cada vez más, la empresa comercializará sus conocimientos y experiencia en la logística, el procesamiento de datos y la fabricación como un servicio a terceros.
Dos retos penden sobre la cabeza del proyecto de fábrica inteligente de Bosch y estas ambiciones más amplias. El primero consiste en encontrar suficientes trabajadores capaces de operar sistemas de fabricación cada vez más impulsados por datos. El segundo será crear estándares de industria para que tales sistemas puedan colaborar entre sí.
Las repercusiones financieras son demasiado importantes para permitir que cualquiera de estos obstáculos impida los progresos. En Alemania, los costes de la mano de obra y de la energía han subido, y el aumento de la automatización y de la eficiencia en como negocios como Bosch preservarán su rentabilidad en el futuro. Como dice Assmann, la adopción de la industria conectada no es opcional, "es una obligación".
Descubre la lista completa de las 50 empresas más brillantes de 2016 de MIT Technology Review