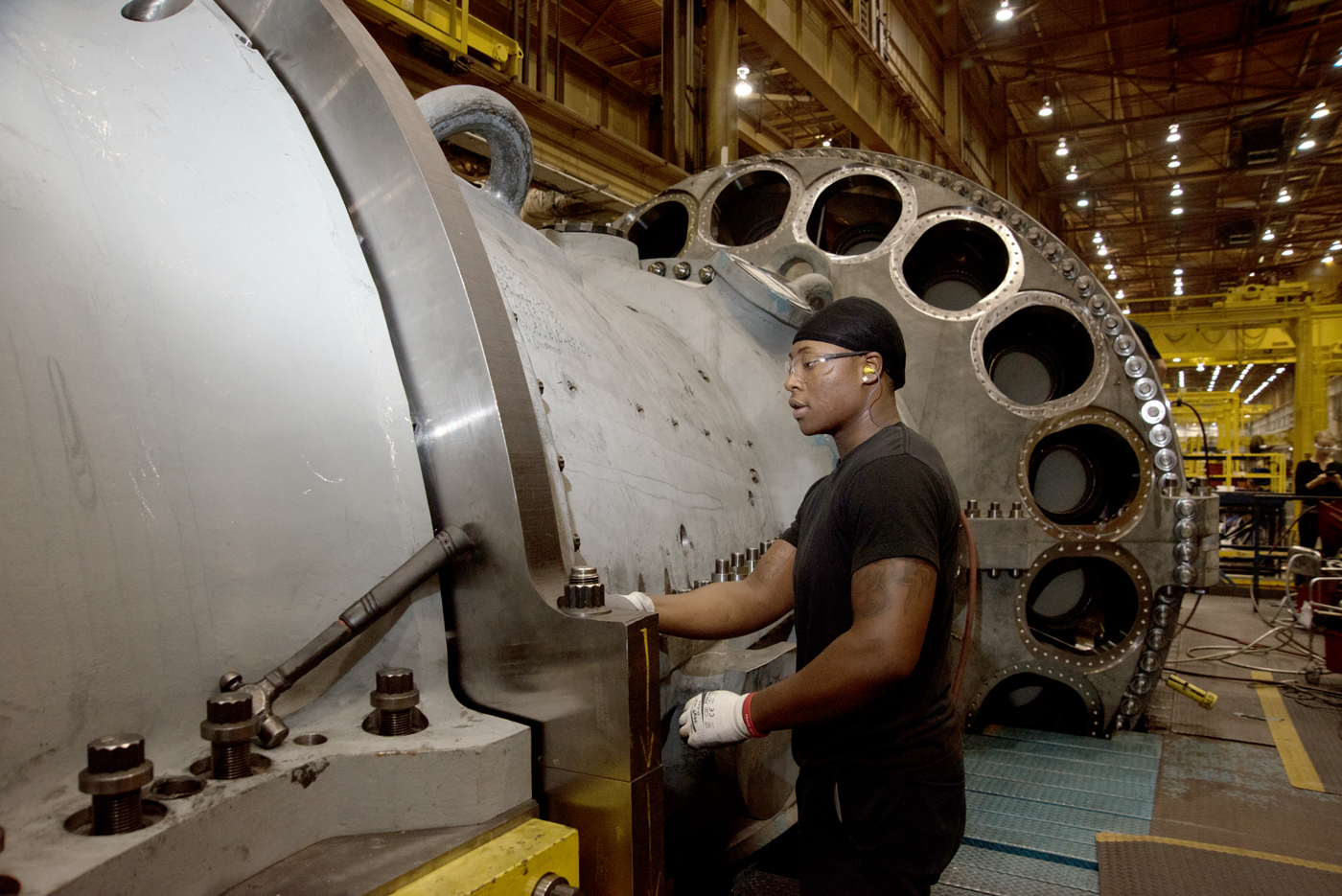
Tecnología y Sociedad
GE construye un puente para que la innovación no acabe en 'valle de la muerte'
El gigante de fabricación ha colocado unas instalaciones de I+D junto a una fábrica de 48 años de antigüedad. El objetivo es que las nuevas ideas no acaben en el olvido y se prueben lo antes posible
Los techos de la sala principal de la planta energética de General Electric (GE) en Greenvile (EEUU) miden 20 metros de alto y el espacio tiene el largo de varios campos de fútbol. Aquí los trabajadores montan pesadas turbinas de gas que de más de tres metros de ancho y unos nueve metros de largo y pesan hasta unos 250.000 kilogramos. Cuando se instala en una planta energética convencional, la más grande de estas turbinas puede generar electricidad suficiente para alimentar unos 500.000 hogares estadounidenses. El complejo trabajo de montar una turbina puede llevar seis semanas.
En la esquina de un edificio cercano, se está creando algo mucho más pequeño. Una de las cientos de piezas que componen una turbina de GE, llamada un flex tip (punta flexible), es más pequeña que una lata de refresco. Esta pieza, que es clave para el sistema de combustible de una turbina, es importante tanto por cómo fue diseñada y fabricada como por el papel que jugará dentro de una turbina.
Foto: GE muestra su proceso de fabricación aditiva. Crédito: General Electric.
La punta flexible es uno de los primeros productos que sale del nuevo centro de I+D de la empresa, y es un ejemplo de cómo GE, uno de los fabricantes más grandes del mundo, intenta actualizar forma de innovar y comercializar nuevas tecnologías. Ubicar sus instalaciones de investigación para la fabricación avanzada al lado de una planta energética es una apuesta de la empresa por que las ideas que surjan en la planta tengan mayores probabilidades de colarse en el laboratorio para su desarrollo. Esto permitirá que las nuevas ideas se prueben y entren en producción mucho más rápido.
Todo esto es urgente. Los clientes esperan que GE acelere la innovación, afirma el director del centro, Kurt Goodwin. El responsable describe las instalaciones como "un puente que atraviesa el valle de la muerte, con centros de innovación que generan buenas ideas en un lado y la capacidad de producción para ponerlas a punto en el otro". Una innovación puede quedarse atascada a mitad de camino durante una década, afirma.
Costó casi 67 millones de euros arrancar el puente de GE, un edificio de casi 12.000 metros cuadrados llamado Advanced Manufacturing Works. Su entrada es un escaparate de las tecnologías de fabricación que está probando GE: impresoras 3D, láseres, brazos robóticos, y más. Justo detrás de los expositores, una puerta se abre hacia un espacio de fábrica abierto con altos techos y suelos de cemento. Aquí investigadores e ingenieros están liderando conjuntos de experimentos, intentando encontrar formas de emplear estas tecnologías para resolver necesidades de negocio específicas.
La nueva punta flexible es una de las primeras ideas prometedoras en lograr cruzar el campus con destino a la fábrica de turbinas para ponerse en producción. La ingeniera de fabricación aditiva Kassy Hart fue la encargada de averiguar cómo fabricar la nueva pieza. El diseño, que incluye largos y pequeños agujeros debajo de la superficie metálica, ayuda a que la pieza funcione de manera más eficiente. Habría llevado mucho tiempo fabricarla si GE hubiese intentado emplear el proceso de fabricación convencional de fundición de metal. En su lugar, la punta flexible está siendo producida mediante la fabricación aditiva con una impresora 3D.
Es la primera pieza que GE, que ha dado mucha prioridad a la fabricación aditiva por toda la empresa, está produciendo en Greenville para sus turbinas.
El equipo de Hart solo tuvo seis meses para ponerlo en producción, y eso requirió mucho ensayo y error. Tardó cinco de ellos en fabricar una pieza que cumpliera con los estándares, pero ahora la línea de producción opera a capacidad máxima con 10 impresoras y un 95% de las piezas que los cumplen. La responsable afirma: "Creo que todos hemos de pasar por ese modo de fracaso antes de poder aprender y adaptarnos".
Cada impresión tarda 60 horas y requiere operar múltiples máquina de manera consecutiva. Durante una visita guiada de las instalaciones en agosto, una pareja de operadores y un encargado supervisaban todas las máquinas. Vestidos con petos y aparatos de respiración artificial, los operadores asisten a las impresora, que se muestran como grandes máquinas cuadradas con una puerta de cristal en una esquina que se abre hacia la cámara de impresión. Las limpian, las llenan de cromo-cobalto y otros materiales de impresión y monitorizan sus progresos.
Con el éxito de la punta flexible, el equipo de Goodwin está probando nuevas ideas que podrían incluir a la línea de impresión. Hoy, según Goodwin, el reto no consiste en encontrar tanto en encontrar buenas tecnologías con las que fabricar sino más bien lograr que las personas que siempre han hecho las cosas de una manera determinada amplíen su forma de pensar.
El responsable concluye: "Nuestra propia gente tiene que aprender a pensar de forma distinta acerca de lo que se puede fabricar".